Investigation of germination effect on the quality of alloy products
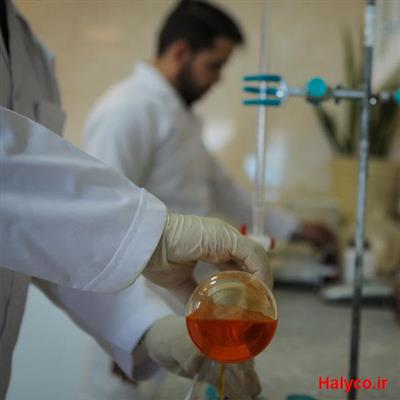
Gray cast iron is an alloy based on the iron and carbon system as well as a number of other elements, the most important of which are silica, manganese, sulfur, and phosphorus. It is distinguished from steels by creating eutectic components in the cast state.
The structure of graphite in gray cast iron may change greatly due to changes in melting, germination, freezing rate, and the influence of some elements, albeit minor (but critical).
Gray cast iron has the highest consumption among cast irons and its production alone is many times more than other types of cast metals. The name of this cast iron is taken from the gray color of its breaking section, which is due to the presence of sheet graphite.
Gray cast irons have relatively good mechanical properties, excellent machinability, optimal abrasion resistance and high vibration absorption.
A clear reason for their excellent properties in the manufacture of complex parts such as parts used in the automotive industry, tractor parts, etc. with a relatively low cost.
When the chemical composition of the melt is in the row of gray cast iron and the cooling range of the melt is within a certain range, the carbon in the cast iron (during freezing) is separated from the melt and laminated in the solidified part, hence the name Gray cast iron is also called sheet graphite cast iron.
The characteristics of gray cast iron depend on the size, amount and distribution of the sheet graphites and the relative hardness of the background on which the graphites are distributed. These factors are generally reduced by the amount of carbon and silicon along with the rate at which the melt and parts cool.
Inoculation operation:
The silica content of the primary cast iron is kept low enough that the silica entering the melt through the magnesium alloy as well as through the inoculation operation brings the total amount of silica content to the desired range. The amount of silicon in the primary cast iron is in the range of 1% to 18% and this amount depends on the type of magnesium alloy that is added to the melt. The low level of silicon in the primary cast iron makes it possible to add some silicon when adding magnesium alloy to the melt and to inject some silicon up to more than 0.6% as the germ material into the melt.
The shape, size, and distribution of graphite in cast irons depend on the number of buds present in the melt before solidification begins. Germination and growth of graphite is done on this bud and therefore, the more the number of these buds, the more graphite is created and as a result, these graphites become smaller.
These sprouts are supplied by elements called inoculants, in the amount of 0.1% to 1% added to the cast iron melt (the usual amount is between 0.2% to 0.5%).
The purpose of the inoculum is to prevent the formation of iron carbide and to encourage graphite production and to control the shape, size and distribution of graphite in cast irons. Consumption of these germination agents is mostly limited to cast irons with a hypovetotic composition because their effect on hypovitic cast irons is far less or even ineffective.
In addition to the above properties, the use of inoculants increases the strength, reduces defects in castings such as shrinkage cavities and reduces the amount of feed used and increases the fluidity of the melt.
There are two basic methods of germination, one is to germinate in a pot and the other is to germinate in the last possible step. Germination in the last stage is any inoculation method that is after leaving the melt from the pot to the mold.
The effectiveness of a germinator is measured by the germination ability of its effects during the interval between inoculation and completion of eutectic freezing.
Advantages of germination include a tendency to reduce whiteness formation in thin sections, greater structural uniformity, avoidance of fine super-refrigeration graphite which is associated with the advantage, and elimination of coarse graphites in thick sections. By germination, low carbon equivalent gray cast irons can be cast without the risk of semantite formation.
The application of germination methods in the final stages leads to the actual or potential removal of the mirage. Using this germination causes less germination consumption and therefore saves money. On the other hand, the germinator makes less change in the composition of cast iron and enables it to use more return in charge to produce unbreakable cast iron inoculated with magnesium ferrosilicon, thus saving more.
- I liked this content:
- 0 |
- View Count: 47
- Number of Comments: 0